Complete Guide to Dynamixel Motors
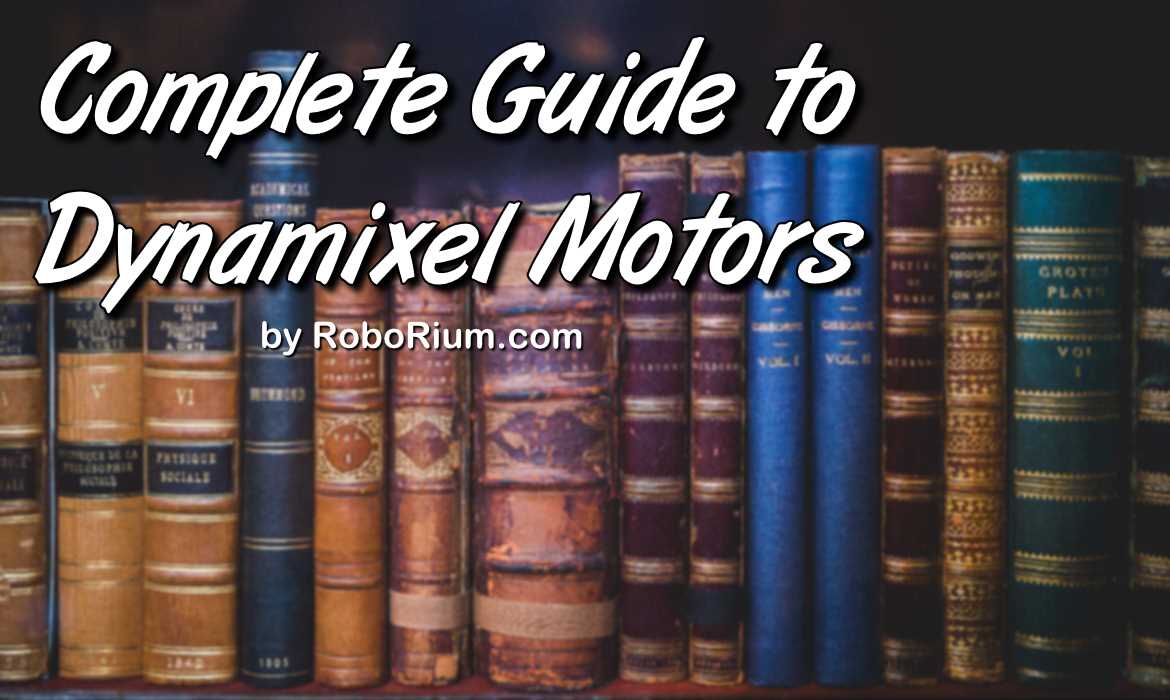
Complete Guide to Dynamixel Motors
Dynamixel is a robot exclusive smart actuator with fully integrated continuous rotation servo motor, reduction gearhead, controller, driver, network in a single module. This guide will help you figure out the best one suited for your application. All dynamixel motors have daisy-chaining capabilities which means they can be connected to each other in series without having a direct connection to a central control circuit board.
Dynamixel X-Series is a new line-up of high performance motors for building multi-joint robots with reliability and expandability. The naming convention for Dynamixel X is:
XL/XM/XH: Low Cost/Mid-Level Performance/High Performance ; 320/430/540: Dimensions
W/V: 12V/24V Operating Voltage ; 350/210: 350:1/210:1 Gear Ratio ; R/T: RS-485/TTL Interface
The XL-series and XC-series mentioned below include the 2XL- and 2XC- motors as well respectively. The "XL-series" does not include the XL-320 motor.
Control
All Dynamixel motors can be controlled using only one of the 2 protocols: TTL or RS485. TTL motors are 3 pin (GND, VDD, DATA) motors while the RS485 motors have 4 pins (GND, VDD, DATA+, DATA-) for communication.
Voltage
Dynamixel Motors usually operate best at their recommended voltages. The possible recommended voltages for these motors are: 7.4V, 11.1V, 12V, 24V.
Only XL-320 runs at 7.4V while all other dynamixel motors are divided into the other 3 categories.
Dynamixel Encoder Steps
The biggest advantage of using Dynamixel motors is the encoder resolution it provides for each range of motion.
For AX-series and XL-320, the 300° range of motion is divided into 1024 steps giving a resolution of 300/1024 = 0.2930° for each step moved.
For other motors with 360° position control in joint mode, the available steps and the resolutions they provide are:
4096 steps = 0.08789° ≈ 0.0879°
502834 steps = 0.0007159° ≈ 0.0007°
526374 steps = 0.0006839° ≈ 0.0007°
607500 steps = 0.0005925° ≈ 0.0006°
1003846 steps = 0.0003586° ≈ 0.0004°
Operating Mode
Wheel or Velocity or PWM (Voltage) or Torque (Current):
In Wheel mode of AX-series, MX-series, and XL-320 the motor runs endlessly with infinite uncontrolled revolutions and acts as a normal DC motor with no position feedback.
Some motors may rely on one of the parameters to better control their speed:
In Velocity Mode of XL-series, XC-series, XM-series, XH-series this mode controls velocity and is identical to the Wheel Mode above. This mode is ideal for wheel-type robots.
In Velocity Mode of PM-series, PH-series it controls velocity and current, but does not control position.
In Current Control Mode of XH-series, XM-series, PH-series, PM-series the motor only controls current (torque) regardless of speed and position. This mode is ideal for a gripper or a system that only uses current (torque) control or a system that has additional velocity/position controllers.
In PWM (Voltage) Mode of XL-series, XC-series, XH-series, XM-series, PH-series, PM-series directly controls the speed with PWM (Voltage) signal.
Joint Mode 0-300° where the Dynamixel acts as a servo operating in the 0-300° range with position feedback. AX-series motors and XL-320 operate in 0-300° range by default.
Joint Mode 0-360° or Position Control Mode is where the Dynamixel acts as a servo of 0-360° range with position feedback but stops after one full revolution. This is ideal for articulated robots where each joint rotates less than 360°.
MX-series, XL-series (except XL-320), XC-series, XM-series, XH-series, PH-series,PM-series, operate in 0-360° range by default.
In PH-series motor this mode controls position, velocity and current.
Multi-Turn Mode in MX-series where the motor can complete (±)28 revolutions with position feedback in either direction (CW[+] or CCW[-]) of the 0th position, 56 revolutions in total, before it comes to a stop. Ideal for multi-turn wrists or conveyer systems or a system that requires an additional reduction gear.
Extended Position Control Mode where the Dynamixel can complete 256 revolutions with position feedback in either direction (CW[+] or CCW[-]) of the 0th position, 512 revolutions in total, before it comes to a stop. This mode is ideal for multi-turn wrists or conveyor systems or a system that requires an additional reduction gear.
In Extended Position Control Mode of Xl-series, XC-series, XH-series, XM-series it controls the position and 512 turns are supported (-256[rev] ~ 256[rev]).
In Extended Position Control Mode of PH-series, PM-series the number of revolutions are not limited.
In Current-based Position Control Mode mode of XH-series, XM-series it controls both position and current (torque) and up to 512 turns are supported (-256[rev] ~ 256[rev]). This mode is ideal for a system that requires both position and current control such as articulated robots or grippers.